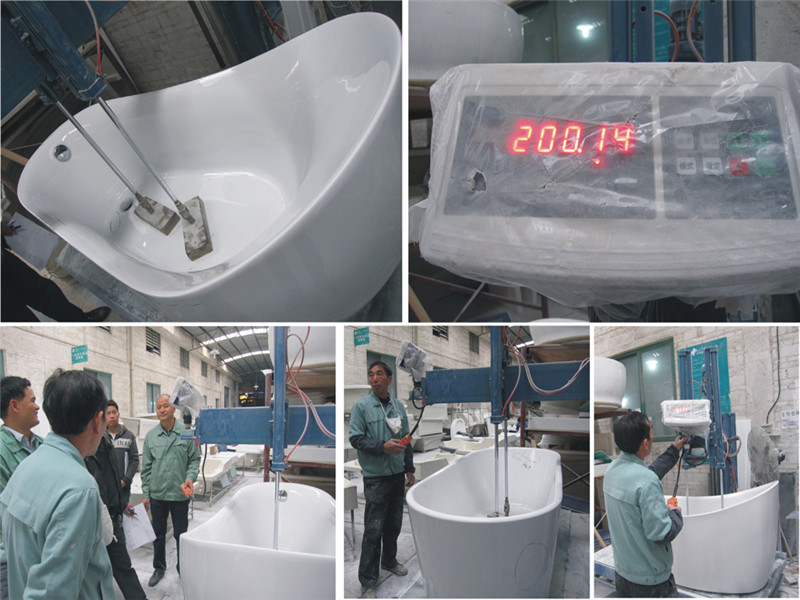
Some knowledge about acrylic bathtub
Bathtubs are a type of sanitary ware products often used in modern home bathroom decoration. The materials used are also quite rich. Generally, ceramic and acrylic materials are mostly used. Acrylic bathtubs are more energy-saving and environmentally friendly, so they are also popular among people. Love, but the production process of acrylic bathtubs is also quite complicated. Today, I will give you a detailed explanation of the production process of acrylic bathtubs, hoping to help more people understand and understand acrylic bathtubs.
1. Molding: The molding of bathtubs, shower room chassis, back panels and other sanitary wares are usually formed by blister or composite board plastic plates. Because bathtubs and other products have a complex appearance and have a deep molding height, they are used by ordinary packaging materials. The materials and machinery are difficult to meet the process requirements, so the selection of appropriate plates and the selection of appropriate equipment are the basis for excellent sanitary ware molding.
2. Sheet: The plastic sheet for sanitary ware molding mainly uses pure acrylic material or A BS composite material, as well as newly developed thermoplastic materials. The special acrylic sheet used for sanitary ware has excellent surface finish, its wear resistance is equivalent to aluminum, it is not easy to scratch, and it is easy to clean, and if accidental scratches occur on the surface, just use polishing agent, you can quickly and easily repair and restore.
3. Mould: According to the design drawings or actual samples of sanitary ware molding, design and process the blister molding mold in actual production. The blister molding mold generally uses aluminum alloy or resin mold. The aluminum alloy mold has a long life, good process characteristics and high surface finish. However, due to the high cost and long processing cycle, the application in the production of conventional sanitary ware products is subject to certain restrictions.
4. Vacuum forming: heat the cut sheet as required in the furnace of the blister forming machine to soften the acrylic sheet, the general temperature is 180-220 degrees, and the composite sheet is generally 140-190 degrees) The softened sheet is mechanically pressed in On the mold, under the condition of in-mold sealing, through compressed air or vacuum blowing and suction, the sheet is thermally stretched and deformed and adsorbed on the mold wall. The cooling fan is started according to the time to make the sheet hard and formed, and then demolded. The product is taken out.
5. Adhesive: The molded blank should be strengthened by resin adhesion. The so-called adhesion is generally combined with unsaturated resin and glass fiber on the bottom of the sanitary ware blank to make the molded product have sufficient strength. Generally, there are two kinds of application methods: mechanical spraying and manual application. Mechanical spraying uses a special spray gun to spray the resin and the cut glass fiber onto the bottom surface of the sanitary ware, and then flatten it with a robot or a manual roller. At present, most sanitary ware production uses mechanical application methods. After the application is completed, it is best to put it in a constant temperature curing oven at 4050℃-the drying room is fully cured, and the deformation of the product after constant temperature curing will be significantly reduced in the future.
6. Edge trimming: After the adhesive product is cured, trimming and cutting will begin. Manual cutting is laborious, quality is difficult to guarantee, and safety hazards are serious.
7. Hole drilling: If the holes on the bathtub and other sanitary wares are on a flat surface, they should be processed with machinery as much as possible, such as multi-hole drills. The device holes on the side of the nozzle, etc. can be processed by a machining center or a mechanical arm. However, due to the relatively expensive equipment, most of them are manually operated.
8. Grinding: The device hole on the sanitary ware should be ground to prevent water leakage. Use a special sharpening head. The adhesive layer on the back of the sanitary ware grinds out a ring-shaped device plane, which is more conducive to the leak-proof protection of the fittings. This process cannot be ignored.
9. Bracket: Sanitary ware brackets are made of solid wood, plastic, steel structure and other materials, of which stainless steel square pipes are mostly used. When applying the adhesive, fix the pad or frame of the mounting bracket on the proper position of the product, and then install the bracket with screws or clips. The quality of the sanitary ware bracket affects the safety of the user. Therefore, the bracket of the sanitary ware must be made strong and stable.
10. Assembly: Water fittings and electrical appliances should be waterproof to ensure safety.
1. Molding: The molding of bathtubs, shower room chassis, back panels and other sanitary wares are usually formed by blister or composite board plastic plates. Because bathtubs and other products have a complex appearance and have a deep molding height, they are used by ordinary packaging materials. The materials and machinery are difficult to meet the process requirements, so the selection of appropriate plates and the selection of appropriate equipment are the basis for excellent sanitary ware molding.
2. Sheet: The plastic sheet for sanitary ware molding mainly uses pure acrylic material or A BS composite material, as well as newly developed thermoplastic materials. The special acrylic sheet used for sanitary ware has excellent surface finish, its wear resistance is equivalent to aluminum, it is not easy to scratch, and it is easy to clean, and if accidental scratches occur on the surface, just use polishing agent, you can quickly and easily repair and restore.
3. Mould: According to the design drawings or actual samples of sanitary ware molding, design and process the blister molding mold in actual production. The blister molding mold generally uses aluminum alloy or resin mold. The aluminum alloy mold has a long life, good process characteristics and high surface finish. However, due to the high cost and long processing cycle, the application in the production of conventional sanitary ware products is subject to certain restrictions.
4. Vacuum forming: heat the cut sheet as required in the furnace of the blister forming machine to soften the acrylic sheet, the general temperature is 180-220 degrees, and the composite sheet is generally 140-190 degrees) The softened sheet is mechanically pressed in On the mold, under the condition of in-mold sealing, through compressed air or vacuum blowing and suction, the sheet is thermally stretched and deformed and adsorbed on the mold wall. The cooling fan is started according to the time to make the sheet hard and formed, and then demolded. The product is taken out.
5. Adhesive: The molded blank should be strengthened by resin adhesion. The so-called adhesion is generally combined with unsaturated resin and glass fiber on the bottom of the sanitary ware blank to make the molded product have sufficient strength. Generally, there are two kinds of application methods: mechanical spraying and manual application. Mechanical spraying uses a special spray gun to spray the resin and the cut glass fiber onto the bottom surface of the sanitary ware, and then flatten it with a robot or a manual roller. At present, most sanitary ware production uses mechanical application methods. After the application is completed, it is best to put it in a constant temperature curing oven at 4050℃-the drying room is fully cured, and the deformation of the product after constant temperature curing will be significantly reduced in the future.
6. Edge trimming: After the adhesive product is cured, trimming and cutting will begin. Manual cutting is laborious, quality is difficult to guarantee, and safety hazards are serious.
7. Hole drilling: If the holes on the bathtub and other sanitary wares are on a flat surface, they should be processed with machinery as much as possible, such as multi-hole drills. The device holes on the side of the nozzle, etc. can be processed by a machining center or a mechanical arm. However, due to the relatively expensive equipment, most of them are manually operated.
8. Grinding: The device hole on the sanitary ware should be ground to prevent water leakage. Use a special sharpening head. The adhesive layer on the back of the sanitary ware grinds out a ring-shaped device plane, which is more conducive to the leak-proof protection of the fittings. This process cannot be ignored.
9. Bracket: Sanitary ware brackets are made of solid wood, plastic, steel structure and other materials, of which stainless steel square pipes are mostly used. When applying the adhesive, fix the pad or frame of the mounting bracket on the proper position of the product, and then install the bracket with screws or clips. The quality of the sanitary ware bracket affects the safety of the user. Therefore, the bracket of the sanitary ware must be made strong and stable.
10. Assembly: Water fittings and electrical appliances should be waterproof to ensure safety.